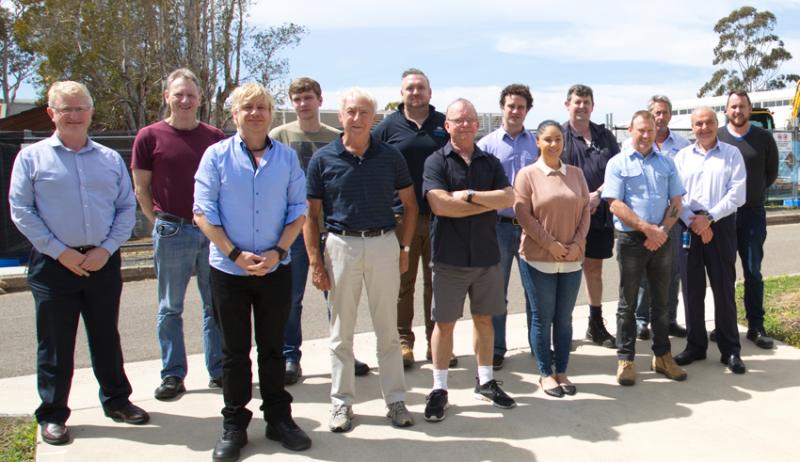
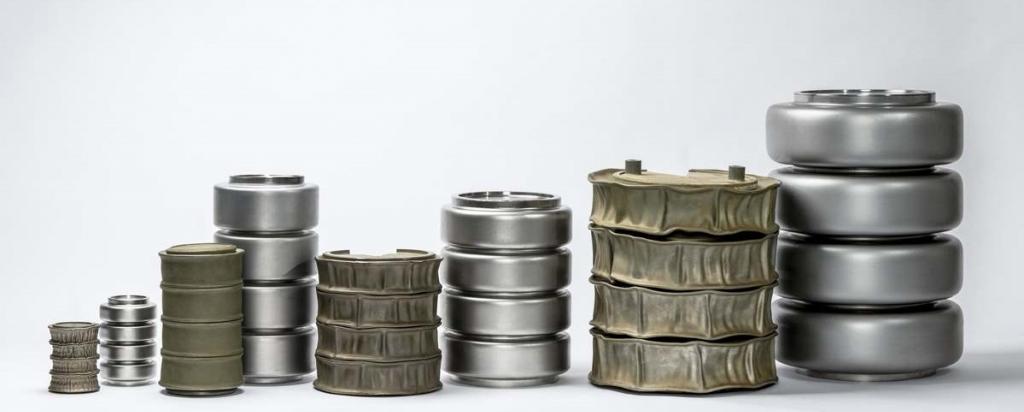
Published on the 9th April 2019 by ANSTO Staff
ANSTO’s new facility uses ANSTO Synroc technology to immobilise waste from the production of molybdenum-99, known as SyMo, is a global, first-of-a-kind operational Synroc plant.
Molybdenum-99, produced in the OPAL multipurpose reactor, is the precursor of technetium-99m, the most commonly used nuclear imaging radiopharmaceutical.
“Today, ANSTO Synroc combines waste form design and process technologies to immobilise and terminate nuclear wastes creating a technology tailored for intermediate level liquid waste. It is also a flexible platform technology that can be modified to suit other waste streams,” according to Technical Director, ANSTO Synroc, Gerry Triani (pictured below back row, first on left)).
“Although our demonstration plant has been commissioned processing hundreds of kilograms of simulated waste, a fully operational plant treating nuclear waste is the game-changer.”
“We have demonstrated an engineering-scale process technology using surrogate chemistry. This provides an example of an operational plant to prospective clients of the ANSTO Synroc technology and gives us added credibility,” said Triani.
ANSTO Synroc is an innovative technology that was developed at ANSTO over many years. It integrates the design of both the waste form and process technology to immobilise and terminate nuclear waste, minimise volume and provide an extremely durable and safe solution for final storage of radioactive waste.
In this operation, ANSTO Synroc will process the intermediate level liquid waste from nuclear medicine production that will be safely piped underground directly to the waste treatment plant from the new molybdenum-99 production facility.
Construction of the Synroc waste treatment plant commenced in the third quarter of 2018 and is anticipated to be completed in the first quarter of 2020.
The liquid waste is pumped from an underground holding tank to a high point in the shield enclosure, where it is injected into the process chamber.
The stream is intimately mixed with the Synroc additive to form a granular powder.
The powder cascades into a thermal processing unit before being dispensed safely to a stainless steel canister.
The canister is then subjected to hot isostatic pressing, which consolidates the powder into a durable solid and reduces its volume.
“Using gravity to cascade the processed wasteform to the canister is a neat solution that produces powder on demand and reduces the radiological load within the facility,” said Triani.
The new plant will be fully automated, with operations being monitored remotely from a control room.
“Our engineers have designed an elegant automated process control system that monitors plant performance allowing the plant to run effectively,” explained Triani.
That automation extends to HIP processing, which will be the first example of the technology being used in a nuclear process environment.
“The HIP system that we have commissioned is unique in its own right. In traditional applications, workers are used for loading and unloading parts into the HIP vessel. Our system has an automated part loading system that lifts the canister into the chamber and unloads it following processing.”
Building construction is expected to be completed early next year with the handover of the facility to commence fit out and pre-commissioning phase of the plant.
“Once the equipment is placed in the shielded enclosure we will conduct performance tests at a unit operations level. Then we will move towards fully integrated testing to ensure that the entire end to end process functions is tested.”
Following that, ANSTO confers with the regulator, ARPANSA for a cold commissioning license.
During cold commissioning, a stream that simulates the waste but is not radioactive is run through the plant to conduct a comprehensive suite of trials.
Once ARPANSA is satisfied that we have met the functional and safety performance requirements stipulated under our license, they will issue a hot commissioning license.
The facility will use legacy liquid waste from molybdenum-99 production during the hot commissioning phase.
The SyMo operational readiness team will be trained at the demonstration plant, which is located in another ANSTO building.
At this time, an internal venture board with several ANSTO executives is overseeing commercial opportunities to support the ANSTO Synroc team.
Triani is enthusiastic about global opportunities for ANSTO Synroc.
“Our technology maturation approach has paid off. We have already had expressions of interest from overseas interests keen to explore our immobilisation technology for other types of nuclear waste streams. We can evaluate those approaches using our knowledge and expertise.”
“We are a lot more mature in providing certainty with respect to the appropriateness of the technology and developing maturation plans for nuclear waste. Our team has developed a systems engineering methodology to address challenging wastes for immobilisation,” said Triani.
In addition to the processing technology, ANSTO Synroc will provide a suite of consumables for the operation.
“We are very confident the process is going to continue to attract global interest,” said Triani.