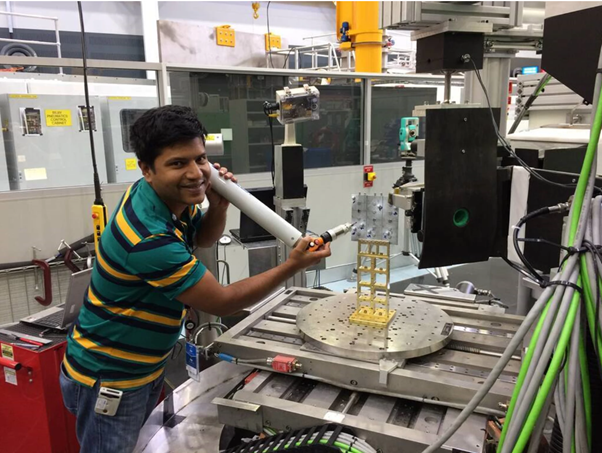
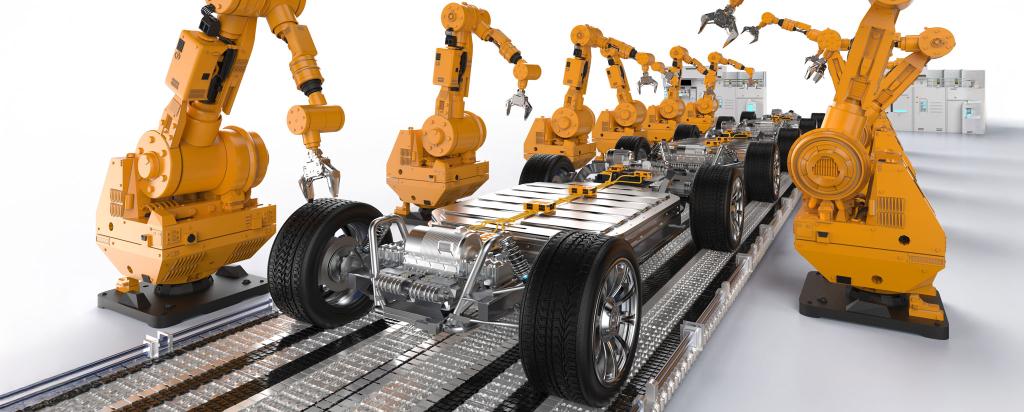
Published on the 13th December 2024 by ANSTO Staff
Dr Rezwanul Haque, now a senior lecturer at the University of the Sunshine Coast, received a national Young Scientist Award for his earlier research using nuclear techniques at ANSTO’s Australian Centre for Neutron Scattering to find cracks and signs of stress in riveted joints in sheet metal in car bodies.
He received the award from the Australian Neutron Beam Users Group, a professional association of scientists who use neutron scattering instruments in their research, at a recent meeting.
“The award highlights 12 years of my neutron beam work, with 15 publications and significant industrial impact, assisted by Federal Government grants worth almost $1million,” he said in a report on the University of Sunshine Coast website.
His interest in self-piercing rivets (SPR), a fixture that joins two or more sheets of material without the need for pre-drilling, began during his PhD studies in 2012.
It is an alternate technique to welding which cannot be used on lightweight alloys, such as magnesium with aluminium alloys or aluminium with advanced high strength steel.
A Self Piercing Rivet (SPR Rivet) is a specialty riveting fixture that joins two or more sheets of material without the need for pre-drilling. A Self Piercing Rivet consists of two main parts: a rivet head with a projection and a hollow rivet body. They are usually made of high-strength steel or aluminium alloys. To install a self-tapping rivet, the tip of the rivet is first aligned with the material to be joined, and then a specialized riveting tool is used to apply pressure to push the rivet head into the material. During the push-in process, the rivet head penetrates the first layer of material and enters the second layer of material, while the shank inside the body of the rivet is extruded to form a diffused shape that fills the gap in the material and creates a strong connection. Source: An Overview of Self-piercing Riveting Process with Focus on Joint Failures, Corrosion Issues and Optimisation Techniques Chinese Journal of Mechanical Engineering Hua Qian Ang RMIT |
The increasing interest in the use of lightweight and high strength ratio materials in vehicle fabrication to reduce the weight of vehicle is due to the urgent need to reduce fuel consumption and greenhouse gas emissions, and hence, is partly the cause of renewed interest in SPR technology, according to Dr Hua Qian Ang of RMIT, who has published on the topic.
“Self-piercing rivets are beneficial for not only for the static load but also dynamic load, which refers to the forces impacting a vehicle that change over time,” explained Dr Haque (pronounced Hok).
When he discovered examples of a self-piercing rivet that looked like a good join, in fact, had a crack inside it, he decided to investigate why the crack formed.
“I thought there must be some residual stresses developing inside the rivet, and the only way to test it involved using the Kowari strain scanner at ANSTO’s Australian Centre for Neutron Scattering.”
He undertook multiple investigations in collaboration with Prof Anna Paradowska, Industry Engagement Manager and ANSTO, Dr Mark Reid (Instrument scientist Kowari) and University of Sydney and A/Prof Yvonne Durandet of Swinburne University of Technology and other associates.
“It's exciting to see novel manufacturing processes being investigated on our neutron strain scanner. Training the next generation of talented scientists and engineers, adding value to their academic and industrial research is in our core mission and we are very proud of the achievements of our users," said Prof Paradowska.
The Australian Institute for Nuclear Science and Engineering provided a grant to support his research.
Neutrons, unlike synchrotron X-rays used in some investigations of lighter materials, can penetrate steel components.
It is believed to be the first time, the technique to detect residual stresses was used on a rivet.
It confirmed that a neutron diffraction measured residual stress profile can be used to predict the presence of cracks in at the tip of SPR rivets that cannot be detected by the normal routine cross-section quality check macrographs.
After validating that it was feasible to use the technique could be applied to a 1mm cube but with an enormous error margin, Dr Haque developed some meaningful parameters to optimise the measurements of residual stresses in rivets.
Rezwanul (Rez) then went on to measure residual stresses in a range of joining combinations, like 2mm, 4mm, 5mm and 6mm thickness in different lengths of rivet and reported the results in a series of publications.
He subsequently used the neutron imaging instrument Dingo to try and assess the best points in the sample to take the measurements.
The investigation using Dingo in collaboration with Dr Ulf Garbe identified a crack in a newly manufactured rivet that appeared to be the result of the manufacturing process.
The finding has great relevance for manufacturers of rivets.
From their earliest use by the Egyptians through the heydays of their use during the period from 1840 to 1930 to the present day renaissance is motor vehicles, the rivet continues to be a small but crucial component.
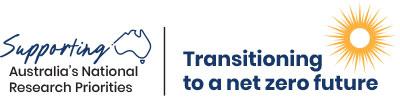
PUBLICATIONS Residual stress distribution in self-piercing rivet joint of high strength steel January 2019 Procedia Manufacturing 30:567-574 DOI: 10.1016/j.promfg.2019.02.080 Residual stress profiles in riveted joints of steel sheets March 2015 Science and Technology of Welding & Joining 20(3) DOI: 10.1179/1362171814Y.0000000272 Optimising parameters for meaningful measurement of residual strain by neutron diffraction in self-pierce riveted joints August 2013 Science and Technology of Welding & Joining 18(6):492-499 DOI: 10.1179/1362171813Y.0000000126 Evaluation of Residual Stress in SPR Joint by Neutron Diffraction January 2012 Feasibility of measuring residual stress profile in different self-pierce riveted joints January 2012Science and Technology of Welding & Joining 17(1):60-68 DOI:10.1179/1362171811Y.0000000076 |